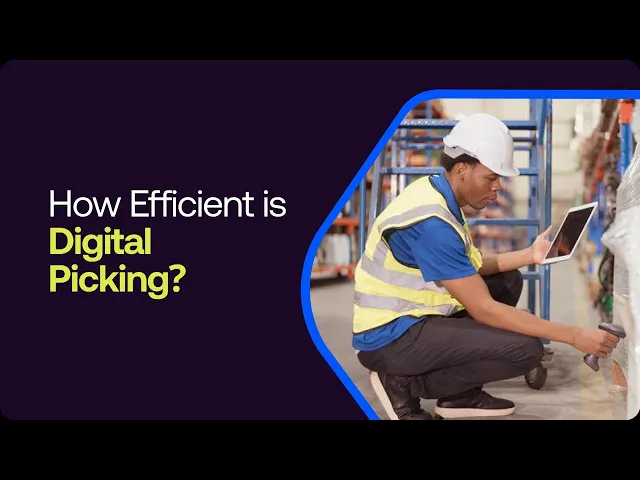
The Ultimate Guide to Barcode Inventory Systems
Share this post
Using a barcode inventory management software can revolutionise accuracy and efficiency in managing stock. Research shows that manual data entry typically results in an error every 300 keystrokes, while barcode scanning errors occur only once every 394,000 scans.
Whether you’re running a bustling eCommerce operation or scaling up your warehouse, implementing a barcode inventory system could be the key to streamlining operations and driving efficiency. With Despatch Cloud, we’re here to guide you every step of the way. In this guide, we’ll cover:
How a barcode inventory system works
How to set up a barcode system
How to implement a barcode system in a warehouse
And of course, we’ll share tips on how Despatch Cloud’s solutions can help you seamlessly integrate barcode technology and optimise your business.
What is a Barcode Inventory System?
A barcode inventory system is a method of tracking products and their movement through the supply chain using barcodes. For over 70 years, barcodes have stored detailed product information, and their utility has only expanded with modern technology. Each SKU’s barcode is unique, staying with the product throughout its lifecycle, providing real-time updates on receiving, storing, and shipping activities.

Type of Barcodes Explained
At Despatch Cloud, we’ve simplified the different types of barcodes you might encounter:
1D Barcodes
These are the classic barcodes commonly seen on retail products. They store data in a single line of characters, making them fast to scan. Common variants include:
UPC (Universal Product Code): A 12-digit barcode mainly used in the US and Canada for retail products.
EAN (European Article Number): Similar to UPC, with 8 or 13 digits, used internationally, especially in Europe.
Code 39: Encodes alphanumeric characters, widely used in manufacturing.
Code 128: A high-density barcode used for shipping labels and logistical applications.
2D Barcodes
These encode information in two dimensions, allowing more data to fit in a smaller space. They’re ideal for industries requiring detailed information, such as logistics and healthcare. Common examples include:
Data Matrix: Used for small items like electronics components and pharmaceuticals.
PDF417: Stores extensive data, often used for ID cards and boarding passes.
QR Codes
Quick Response (QR) codes are rapidly becoming indispensable in eCommerce. They’re used in customer-facing contexts for product details, discounts, and promotions, as well as in warehouses for tracking and accessing product information via smartphones.
Benefits of Barcode Inventory Tracking Systems for eCommerce
A barcode inventory management system offers numerous advantages to your Warehouse Management System, including;
Real-Time Inventory Accuracy & Visibility: With a barcode inventory management software integrated with Despatch Cloud, tracking stock is no longer a guessing game. Every scan provides real-time updates, ensuring you always know your stock levels.
Faster Order Fulfilment: With Despatch Cloud, your warehouse team can scan barcodes to instantly locate items, saving hours of time and speeding up the order fulfilment process.
Cost Reduction: Barcode systems drastically reduce human error, minimising mislabeling and incorrect shipments. This leads to streamlined stock control, reduced return rates and operational costs.
Improved Customer Service: Accurate and timely delivery enhances the customer experience, translating into repeat business, glowing reviews, and increased brand loyalty.
Essential Components of a Barcode Inventory System
Setting up a barcode system may seem daunting, but it’s more straightforward than you might think. Here are the key components:
Barcode Printers
These devices create the barcode labels for your products.
Barcode Scanners
Scanners read the barcodes and transmit data to your inventory management system. Options include handheld scanners, smartphone-integrated scanners, and wrist-mounted devices.
Inventory Management Software
This acts as the brain of the system. A robust solution like Despatch Cloud integrates seamlessly with your barcode system to organise and interpret data in real-time.
Explore options on digital scanning devices...
The Tools that Enhance Digital Picking Efficiency
One of the key areas where technology has revolutionised operations in logistics and warehousing is the picking process. Digital Picking tools not only streamline workflows but also reduce errors, ensuring smooth and accurate order fulfilment. Every warehouse has unique demands, which is why choosing the right tools that adapt to specific needs is critical.

Handheld Scanners: These are the staple in most warehouses, and allow for quick and accurate barcode scanning, making them ideal for environments where hands-free operation isn't required. They are built to withstand the rigors of warehouse operations. For smaller-scale warehouses or those with less complex operations, handheld scanners provide a reliable and cost-effective solution.
Hand Straps: For warehouse staff who need more freedom of movement, hand straps are an excellent accessory. These allow devices to be securely attached to your hand, ensuring they're always within reach while keeping your hands free for other tasks.

Wrist-Mounted Devices: Let's take hands-free to the Next Level! These compact tools sit comfortably on the wrist, providing quick access without needing to carry or hold anything. These devices are perfect for high-speed picking environments, allowing staff to focus entirely on their tasks while still having the technology at their fingertips.
Why Choose Despatch Cloud for your Barcode Inventory System?
Despatch Cloud offers a comprehensive suite of tools designed to make barcode inventory management effortless. With robust barcode scanning, tracking, and reporting features, we enhance warehouse management and efficiency.
Here’s why our customers love Despatch Cloud:
Ease of Use: User-friendly design ensures quick adoption by your team.
Cost-Effective: Helps you save time and resources.
Error Reduction: Minimises mispicks and human error.
Time Savings: Streamlines operations for faster results.
Ready to optimise your inventory management with Despatch Cloud? Let us help you take your operations to the next level with our powerful barcode solutions.